DIE SINK EDM
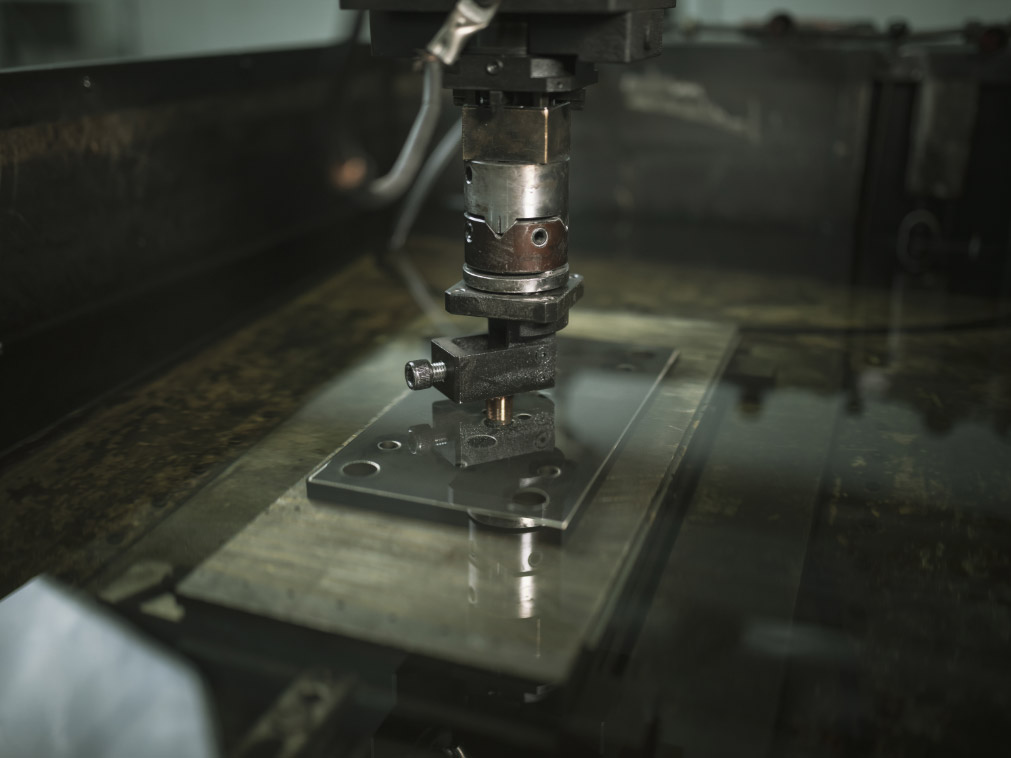
Die sinking EDM is the manufacture of a part by using a copper or graphite electrode with the final design shape. The electrode penetrates the raw material, which must be conductive, until the final shape is obtained. IAM has 2 penetration cutting machines.
Die sinking EDM is the first method used to obtain parts using the EDM process. Its principle is based on an electrode with the inverse shape of the part to be manufactured, which is inserted into the head of the machine connected to the positive pole, which approaching the raw material, connected in turn to the negative pole, creates thousands of direct current pulses, generating an electric arc. This causes the material to erode, and while the electrode penetrates the material, it advances to obtain the required shape throughout the depth. Between the electrode and the part, there must always be a gap filled with dielectric fluid (usually mineral oil or water), so that the impulses are produced and the material can be eroded.
The piece obtained by this cutting technology has three layers: The first layer, or the surface layer, contains tiny metal pieces extracted from the material and small particles from the electrode; the second layer or the white layer is the one that can undergo small changes in the metallurgical structure due to the impulses received by the material; and finally the third layer or the annealed layer is the part of the piece that has been thermally heated without being melted. The state of these three layers defines the quality of the cut, and mostly this is usually altered by the cycles of activation and deactivation of the process, the relationship between these cycles and the total cutting time and finally the size of the previously mentioned gap (the distance between material and electrode).
As for the electrode, it is usually made of graphite or electrolytic copper and, as mentioned above, it must have the inverse shape of the part to be obtained (mirror effect). The fact that you can regulate the distance that you want to penetrate the electrode into the piece, makes it possible to manufacture pieces both in through shapes or as blind shapes.
Penetration EDM is a good process for machining fragile parts since no cutting forces are created. In addition, it is ideal for obtaining microstructures, complex geometries that other technologies cannot access, or extremely fine and delicate surface finishes.