Waterjet cutting process
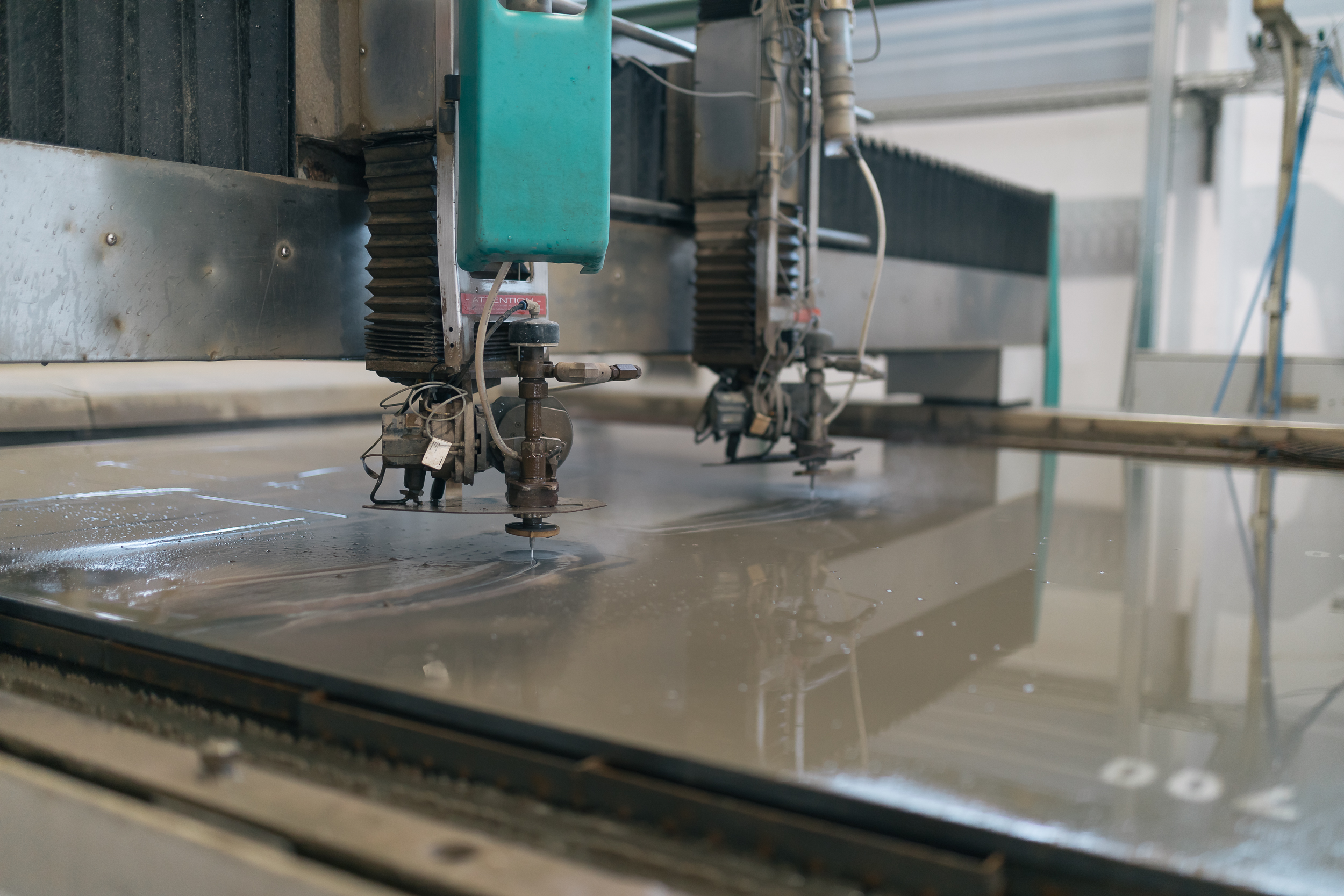
Water jet cutting is a mechanical process in which, by means of the impact of water at high pressure, all types of material are cut to the desired geometry. IAM CUT has 4 conventional water jet cutting machines.
The abrasive water jet cutting technology consists of pressurised water at high hydrostatic pressure (up to 6000 bar) which, when converted into kinetic energy, with abrasive particles of different sand sizes (depending on the application) creates a three-phase jet: Water, abrasive and air. The created jet can reach up to three times the speed of sound (around 1000 m/s) and is thus capable of eroding any type of material in a wide range of thicknesses, achieving any type of geometry.
The basic idea of how the cutting process works is very simple: a flow of water is generated from an ultra-high pressure hydraulic pump and passes through smaller and smaller pipes, transforming hydrostatic pressure into velocity, until it reaches the cutting head. Inside the cutterhead it first passes through a tiny stone orifice (varying between 0.254 and 0.381 mm diameter in conventional cutting) where the water flow is controlled. Once past the orifice, the jet becomes the size of a human hair, and the next step is to add abrasive particles. For this, a specific flow of sand is introduced into the mixing chamber by gravity. The jet of water and abrasive enters the mixing tube from where it exits at high velocity and is capable of cutting materials such as steel over 300 mm thick. The size of the jet, depends on the inside diameter of the mixing tube, which normally has a ratio of three times larger than the orifice. These are usually made of hard metal, and the diameter ranges from 0.76 mm to 1.5 mm.
This manufacturing method has its origins in nature, as it has been proven for thousands of years that water is capable of changing the shape of almost any element by acting on it. However, it was not applied in industry until 1983. The great flexibility of the process meant that its use was extended to different sectors apart from the cutting of parts for engineering.
The productivity, flexibility, low economic cost and the great capacity to machine any material without producing thermal damage to its composition, make waterjet cutting a very good opportunity to move away from conventional machining.