Wire EDM in electric motors for the renewable energy sector
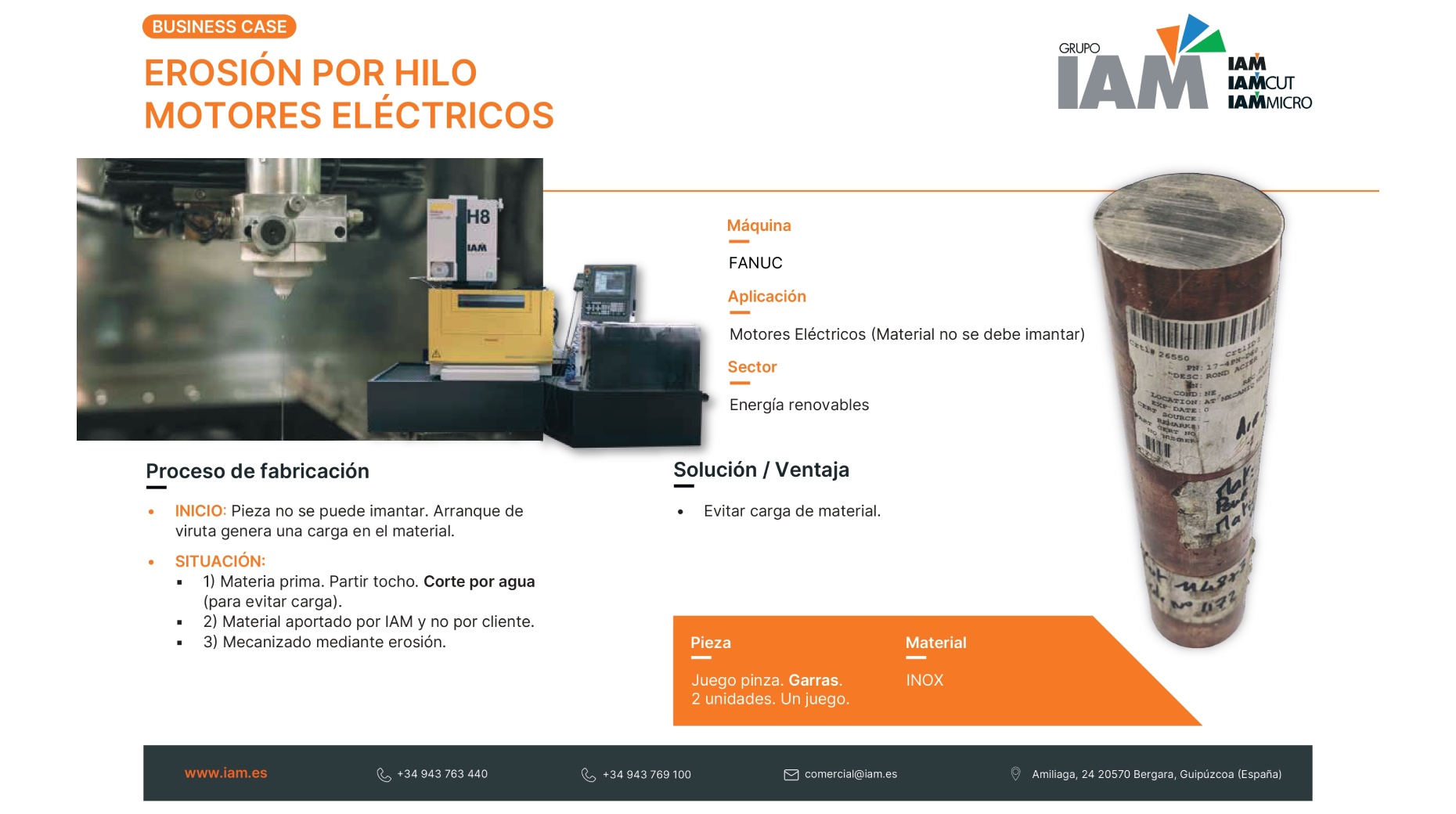
In electric motor manufacturing, innovation and precision are crucial to ensuring that the resulting parts perform well. One technique that has been involved in this process is wire EDM. This method uses a conductive wire to cut complex shapes in conductive materials precisely by harnessing the ability of these materials to conduct electricity and generate the electrical arcs required for the machining process.
This article will dive into a success story in the renewable energy sector, where IAM has demonstrated the transformative potential of wire EDM in producing electric motors.
Wire EDM in electric motors
The Grupo IAM has successfully implemented wire EDM in producing electric motors, in this case with application in the renewable energy sector, specifically in machining critical parts such as the gripper and claw set. The process starts with a raw material that cannot be magnetized due to its magnetic properties.
Waterjet cutting is performed on the billet to avoid loading (magnet) on the material during machining. In addition, IAM was the material supplier, as in many other projects. Once the INOX steel, suitable for electric motors as it cannot be magnetised, has been received, machining employs electroerosion.
The machine used for this process is a FANUC, known for its precision and efficiency in machining operations.
The advantages of EDM
Wire EDM provides several advantages that allow it to be used in parts for the manufacture of electric motors:
High precision in the machining of parts guarantees optimum dimensional and geometrical quality.
Burr-free quality, as unlike other cutting methods, wire EDM does not leave burrs or taper on parts, thus improving efficiency and reducing finishing times.
Capacity for complex shapes and parts with inclination, expanding the design possibilities in manufacturing parts for electric motors.
Machining of hardened materials, providing flexibility in material selection.
It is efficient in production because it can machine several parts at once, thus optimizing production times and improving overall process efficiency.
Grupo IAM, high-precision EDM and cutting work
The case of IAM in implementing wire EDM for manufacturing parts for electric motors highlights the importance of searching for complex solutions, adopting advanced technologies in the industrial field, and selecting suitable materials and their management. All this has not only improved quality and efficiency in production but also positions Grupo IAM as a good option for the manufacture of dies, molds, and unique parts in many different sectors, and wire EDM, with its many advantages, proves to be a valid tool for this. If you want to know more about Grupo IAM or the different types of high-precision cutting, please contact us.